

Autonomous production - New opportunities through AI?
The smart factory: No companies have so far reached the highest level of manufacturing autonomy
"Lights-out manufacturing calls for extensive automation and connectivity within and between production processes. But no one has managed to achieve that so far. Artificial intelligence and advances in automation are now making it much easier to realize."
Artificial intelligence (AI) use cases are becoming increasingly powerful and adopting much more of an applied focus in many fields, including process control. And automation has come a long way in recent years. Both of these developments bring the vision of autonomous production within reach for the first time.
Roland Berger is currently conducting a study on autonomous production systems in discrete manufacturing in order to outline the progress that has been made and identify the key drivers of developments. One conceivable scenario is that future production systems will operate fully autonomously – with machines that are able to optimize themselves, communicate with each other and with a higher-level control system that can even make decisions in the event of malfunctions (reflecting Manufacturing Autonomy Level 5 in the diagram), and also improve the overall process. Experts call this lights-out manufacturing. However, it requires extensive automation and connectivity within and between production processes. So, how far away are we from seeing this vision brought to life? And what contribution can we expect from artificial intelligence and the like? What parts of the future vision are already possible in production today and what elements are still missing? These are the questions that our study examines.
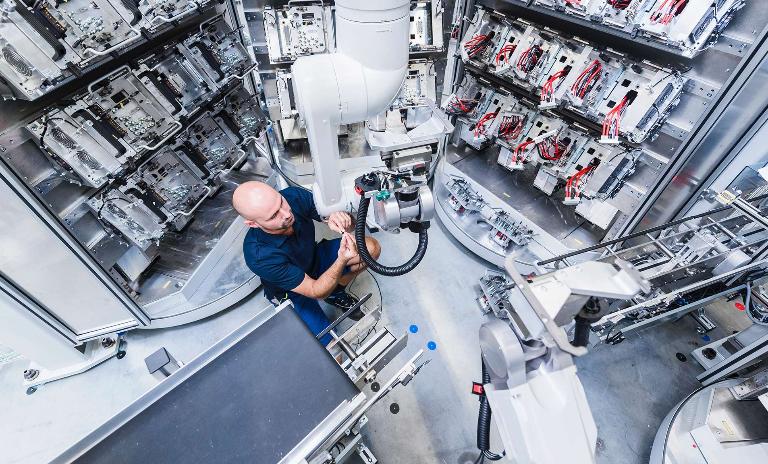
Small and midsize discrete manufacturers in particular have high hopes for autonomous production systems, as mass production here still requires a great deal of manual intervention for tool changeover, assembly, programming and scheduling. Whereas the obstacles to fully autonomous production previously seemed almost insurmountable, relevant key technologies have evolved significantly, with some even reaching market maturity in the meantime.
Based partly on interviews with users, research institutions, technology providers and software companies, our study tests the following hypotheses:
Hypothesis 1: Despite Industry 4.0 being invented in Germany, the highest level of autonomy is found in factories in China
The majority of industry in Germany has reached Manufacturing Autonomy (MA) Level 2. This means that production lines are connected and their processes controlled. Some manufacturers have even reached MA Level 3, including many automotive OEMs and electronics companies.
Although Industry 4.0 was "invented" in Germany and heavily subsidized by the government, other nations have been quick to catch up and are currently pushing the construction of I4.0 production plants and autonomous factories. Electric car production in China is leading the way here.
Because few new factories are built on greenfield sites in Germany, it is much more difficult to design I4.0 factories from the drawing board up. The new "Factory 56" unveiled by Mercedes-Benz Cars is one of the few examples of MA Level 3 to 4 having been reached for an assembly line.
Hypothesis 2: Cloud providers such as Microsoft and Amazon are more focused on production and are driving artificial intelligence forward.
This is particularly true of Microsoft and Amazon Web Services. These companies use their clouds as a platform for manufacturers to implement their use cases. Edge gateways allow use cases implemented in the cloud to be transferred directly into the machine control system. While the cloud providers make the infrastructure available, it is the manufacturers themselves that must implement the specific use cases. AI-enabled use cases include the optimization of machine parameters (e.g. welding parameters) (Level 4), automated self-learning quality control (Level 4), predictive maintenance (Level 4) and dynamic optimization of schedules (Level 5).
Hypothesis 3: Significant production developments such as bin picking or autonomous transport systems are on the verge of a breakthrough.
Two of the most important automation tasks are bin picking (and the subsequent correct placing of parts) and transporting parts from one machine to the next. Both of which are performed by humans without thinking but previously proved virtually impossible to automate. However, progress in automation technology has enabled both tasks to be realized by machines, facilitating more flexibility and autonomy in the factory. A combination of optical scanning systems and robots now enables randomly positioned parts to be picked out of bins, and automated guided vehicles (AGVs) can then move them freely around the factory. Both technologies have evolved rapidly in recent years and are becoming both more powerful and more cost effective. These developments enable factories to make the leap from MA Level 2 to Level 3. In addition to these two capabilities, many other automation technologies have now reached the necessary level of maturity for use on the factory floor.
Hypothesis 4: New safety technologies and modern man-machine interfaces enable ideal cooperation between man and machine.
There will always be tasks that cannot be automated in a factory owing perhaps to the level of cost or the degree of technical complexity. Humans and robots will therefore still have to work together. Examples include robots and humans working side by side in an assembly cell, with humans taking over the tasks that a robot cannot (yet) perform.
At present, such cooperation is still severely restricted by health and safety regulations (e.g. concerning speed or working at head height), but improved safety technology in the robots will make it much easier as time goes on.
Manufacturers that align themselves with the trends outlined in these hypotheses will find that they are in a position to achieve higher levels of autonomy faster in their factories of the future. So far, however, we have not identified any automation or software manufacturers that are specifically working on enabling Level 5 manufacturing autonomy. MES providers are currently working primarily on creating transparency and thus enabling data-based decisions by humans (optimization of machine parameters, schedules, etc.). Cloud providers have made the infrastructure for AI use cases available, but the focus is on Level 4 use cases such as machine parameter optimization. So, is the autonomous factory destined to remain little more than a vision?
Interested in receiving our upcoming study on AI and autonomous production? Register here and we will send it to you upon publication.