

Battery recycling is a key market of the future: Is it also an opportunity for Europe?
Battery manufacturers and OEMs need a clear framework to work within – at European and national level
After a difficult start, the mobility revolution is now taking off. In Germany alone, one million electric cars are set to be on the roads by 2022. That's according to the federal government's latest plan. By 2030, battery-operated electric vehicles and plug-in hybrids will make up around 20 percent of vehicles on the ground globally.
Hand in hand with this development will come a further increase in the demand for lithium, cobalt, nickel and manganese, the key raw materials for the production of battery cells. The demand for large lithium-ion batteries (LiB) will increase the most, rising to around 1,000 GWh by 2025 and at least double that by 2030. This suggests annual growth rates of 35 percent for lithium and more than 50 percent for nickel.
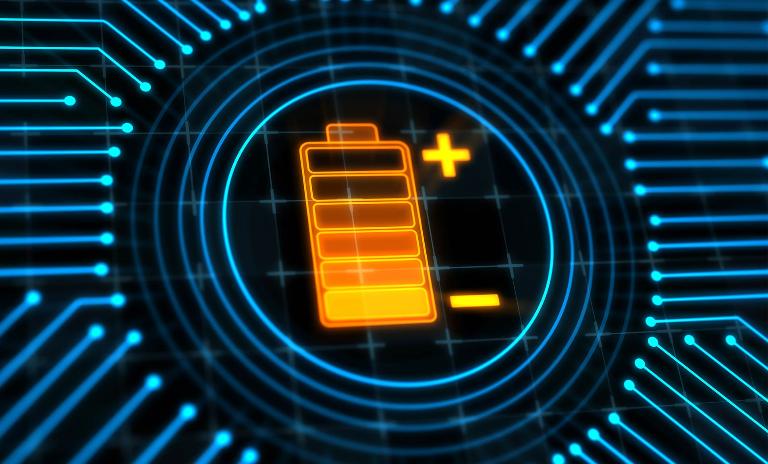
Thanks to new production and refinery capacities, future supply bottlenecks are unlikely. Nevertheless, players must cushion against the continuing price risks that come from the fact that the supply of raw materials and refinery products is highly consolidated within the industry. And they must guard against political risks in the crucial mining countries of Africa, Asia and South America, which were brought sharply into profile once more by the export ban on nickel ore announced by Indonesia at the end of October.
Recycling: An important alternative to primary raw material extraction
Recycling is thus gaining new significance as a topic of interest. The recycling of used electric batteries offers huge potential that has barely been exploited to date. Legislators are also exerting pressure: If the EU Commission, whose new Battery Directive is to be transposed into national law by 2024, gets its way, a much larger proportion of materials will have to be recycled in the future. The Commission wants car and battery manufacturers to establish a comprehensive system of battery collection and recycling. The stated aim is for around half the weight of lithium-ion batteries (LiB) to be recycled.
Two processes dominate industrial recycling at the moment. One is the pyrometallurgical process, in which nickel, cobalt and copper are recovered through smelting. The alternative is to use hydrometallurgical processes where the metallic component and the recycled metal solutions are dissolved by leaching.
The EU has sufficient capacity for polymetallurgical recycling for 2020. Viewed against the target for recovered materials as laid down in the EU Battery Directive, however, the process has its limits: lithium and manganese cannot be recovered efficiently, so it is therefore not particularly economical. The situation is different with hydrometallurgical methods, which for the first time bring a closed loop recycling system within reach. High recovery rates have already been achieved in pilot projects under optimum conditions.
"As this type of vehicle drive becomes more and more common, the recycling of electric car batteries will become increasingly attractive. If Europe is to keep pace here, where it has not before, politicians must now ensure that there is a functioning recycling system and a clear framework within which the industry can operate."
Recycling: Hedging against fluctuating raw material prices
The economic benefits of these recycling processes are therefore very promising. Depending on the composition of the battery cell, the potential net profit from the recycling of a medium-sized battery can be estimated at 12 to 15 euros per kWh, or a total of 600 to 1,1200 euros (see the chart illustrating the costs and revenues from recycling a medium-sized battery pack with the latest cell chemistry NCM811). Based on a recycling rate of 80 percent after ten years of battery use, the recycling market's profit pool (based on the costs of mechanical treatment and hydrometallurgical processes) could amount to EUR 0.7 billion to EUR 1.4 billion in 2030 and EUR 2.4 billion to EUR 4.8 billion in 2040 according to our calculations. Assuming a volume of 1.7 million tons of batteries being recycled in 2030, 250 thousand tons of active materials (nickel, cobalt, manganese, lithium) could also be recovered. This corresponds to around 20 to 30 percent of the EU's cobalt and nickel demand.
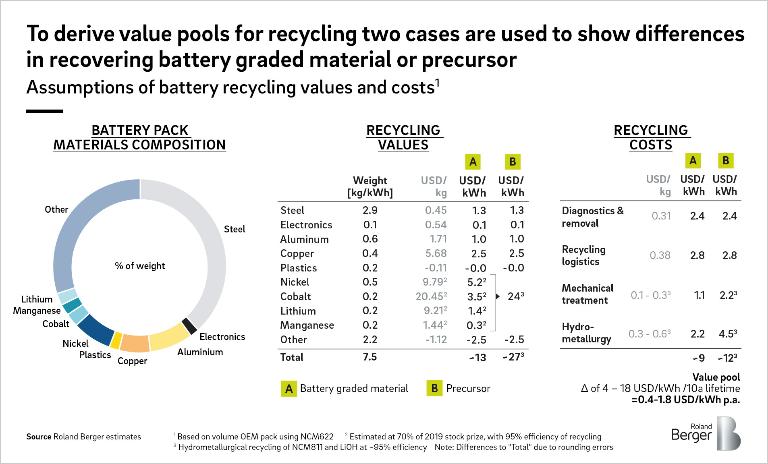
Technology and capacities are centered on China
No wonder there is currently a lot of movement in the market. More and more traditional recycling companies, battery cell manufacturers and producers of cathode materials want to profit from the growth in the coming years. Currently, LiB recycling capacity amounts to less than 100,000 tons worldwide. China occupies a clear pole position: with 67 percent of global production (in GWh output), it is not only a leader in battery production but also in the production of cathode and anode materials and in the refining of the necessary primary materials. China also tops the global rankings for the recycling of battery cells and cathode and anode materials.
Chinese suppliers are at an advantage: They benefit from an already large market, enjoy extensive support from the state and have good access to recyclable materials. Manufacturers of electric vehicles must set up and standardize recycling facilities for batteries. These facilities are shared by manufacturers, battery manufacturers, scrap yards, integrated companies and others. The guidelines published by the Chinese Ministry of Industry and Information Technology (MIIT) at the beginning of November describe two types of recycling facilities that the industry has to set up as needed: smaller recycling centers are mainly used for interim storage and are limited to a total of 5 tons of batteries, larger "concentrated storage facilities" have a minimum capacity of 30 tons and are designed for long-term storage. Plant operators are also expected to use digital technologies to track, collect and share inventory data with producers. The latter must in turn report the recycling data "promptly". Existing plants have six months to meet the requirements of the guidelines.
With at least four "Gigafactories" in Germany and three more in Poland, Sweden, and Hungary planned or already in construction, there are good opportunities for Europe's industry to remain competitive.
To do that, however, the industry needs a clear political framework within which to work. In addition to promoting basic research, which must go beyond the state-of-the-art already achieved in Asia, specifically when it comes to active materials recovery, policymakers need to set standards, for instance on machine-readable information on rechargeable batteries, in order to advance the level of automation in dismantling used batteries and to push the rapid industrialization of recycling processes. Track & trace mechanisms, which are already standard in China today, should be introduced as mandatory and, indeed, standard across Europe. As the European industry seeks to secure access to raw materials and move forward, it is important to consider whether there should be export restrictions on used batteries and active materials to be recycled (known as "black mass"). In order to offer planning security to companies in the industry, the transposition of the new EU Battery Directive into national law should also be dramatically accelerated and the scope for national modifications limited as far as possible. The task for the industry now is to build up the necessary capacities – before Asian competitors take this field, as they have others, and divide it up among themselves.