The Roland Berger model for robust and future-proof operations makes companies adaptable, agile and resilient.


Future-proofing the workforce in manufacturing
Manufacturers must address their labor strategy to remain competitive in a rapidly changing landscape
Manufacturing companies are under pressure. The need to adapt manufacturing labor strategy, tap into the benefits of new technologies, and deal with changes among the workforce has never been greater. But by shaping a future-proof workforce today, manufacturers can position themselves for long-term success.
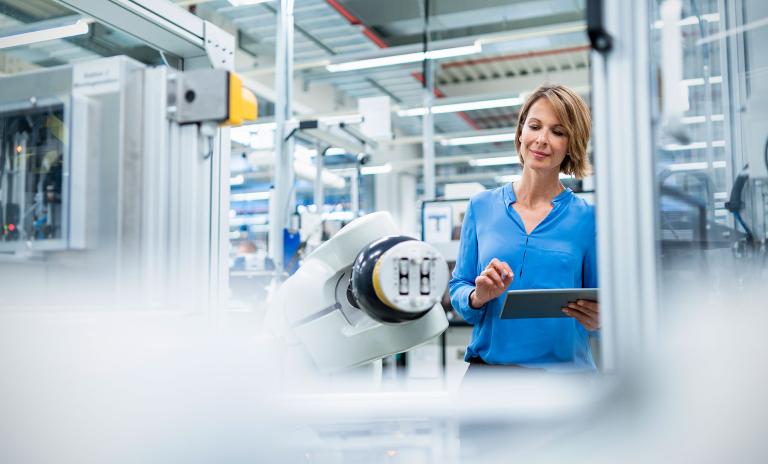
"The way to active workforce management goes through proper diagnostic and projection of workforce and skill demand."
The current challenges are reflected in the declining sentiment of business leaders in many regions. In Germany, for instance, the IFO Business Climate Index has been steadily falling since its post-Covid high in 2021, sinking from 101.7 to 86.6 points.
Labor shortages are now a serious issue. Unfilled positions in Germany are set to cost the nation’s economy around EUR 50 billion in 2024. According to the German Economic Institute, this could rise to EUR 74 billion in 2027 – between 1% and 2% of Germany’s GDP. This does not include the lost opportunities due to lost opportunities, delayed product launches and overworked staff.
Other factors are also at play, including the rise of new competitors, rapid changes in AI technologies, and shifts in global trade networks.
To remain competitive in the global manufacturing landscape, companies need to change. We currently see that manufacturing companies are currently reconsidering their strategy addressing three trends:
- A greater need to adapt production footprints to react to changes such as new tax regulations or raw material availability
- A growing need to prepare for the upcoming shortage of qualified workers
- Increased use of AI and data analytics to rapidly harvest low-hanging fruit and prepare a future-proof infrastructure
Initiatives to create resilience and address these key trends often require both robust action and significant organizational changes. The latter can be especially daunting for many organizations.
Roland Berger can help. We have extensive experience of guiding businesses along an end-to-end process, from defining measures for change to a full restructuring. Our unique value proposition offers a one-stop shop for all your manufacturing and organizational needs.
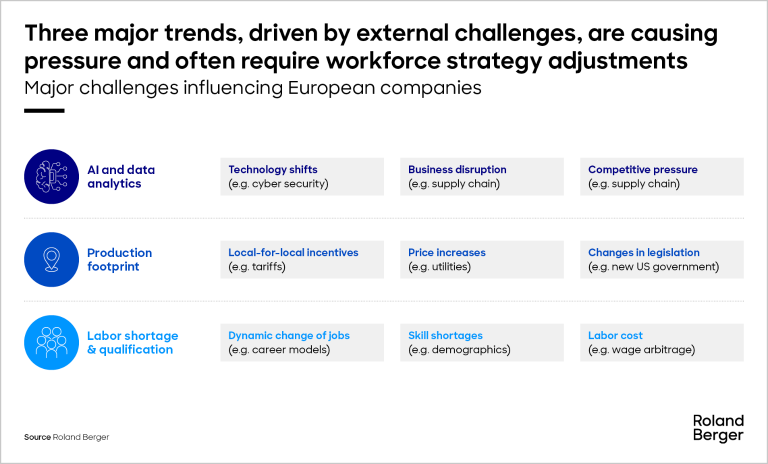
"Organizational changes encompass more than just technology and processes; people and skills are also paramount."
Tailored solutions to optimize production
With our SOP framework we can assess and optimize complex global production networks as well as single production lines by finding tailored solutions.
Working with the SOP framework will shift organizational requirements. New technologies demand new skills from employees, while a revised footprint has an immediate impact on an organization’s headcount. Labor shortages will lead to a continual revision of talent acquisition processes.
A structured approach and rich catalog of supporting assets covers various project archetypes, in line with three main trends:
- Production Strategy: Defining a digital production strategy to lead the digital transformation by implementing AI solutions, IoT technologies, and integrated manufacturing execution system
- Overall network design: Improving footprints by developing relocation concepts, evaluating scenarios, finding the right sites, and providing implementation support
- Plant performance management: Driving efficiency to get the most value from production machines, assets, and labor. This ranges from the rigorous implementation of LEAN methods to designing manufacturing concepts. We support transformations from the shop floor up to the strategic level
"It requires both people and technology investment – Goal is to untap the global talent pool, while making the right technology investment decisions."
A strategic approach to workforce management
Organizational changes encompass more than just technology and processes; people and skills are also paramount. That's why Roland Berger has developed a unique approach to people management with our Strategic Workforce Management solution. It centers around three key areas:
Build up: Invest in new talents and skills
Reshape: Requalify and invest in existing resources
Reduce: Realize changes in business models
Roles and skills profiles in operations are evolving. We help our clients identify what they need for their future operations and determine which employees can be reskilled or redeployed.
One major asset is our AI-based workforce tool, which helps us identify existing skill sets and establish global sourcing and shoring models based on future needs and an intelligent labor supply forecast. This offers increased robustness and valuable support during technological changes. We can also identify capability gaps and the associated upskilling costs or hiring efforts to supplement your strategy with global sourcing and shoring models.
Change often leads to restructuring within organizations. At Roland Berger, the management of changing business models is part of our heritage. Our White Book approach also helps organizations manage complex workforce adjustments with a host of easily deployable tools. It is the basis for an accelerated and efficient negotiation procedure with employees' representatives.
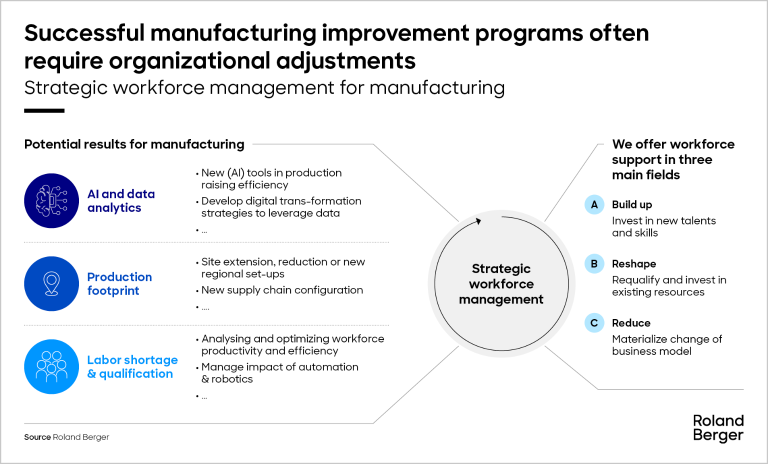
Your partner for organizational change
The right workforce is key to securing a company’s future. Attracting, developing, and retaining top talent is becoming increasingly challenging, which is why our clients trust us to guide them through the complexities of manufacturing and organizational change. From digital strategies and manufacturing footprints to workforce evaluation and talent management, we tailor our solutions to your needs.
Register now to receive regular insights into our Operations topics.