Explore the growing challenges and promising solutions in global waste management. Discover how population growth, consumption patterns, and regulatory initiatives shape the future of municipal solid waste. From regional disparities to the imperative of effective waste management, uncover insights into recycling innovations and investment opportunities. Join the journey towards a cleaner, more sustainable future.

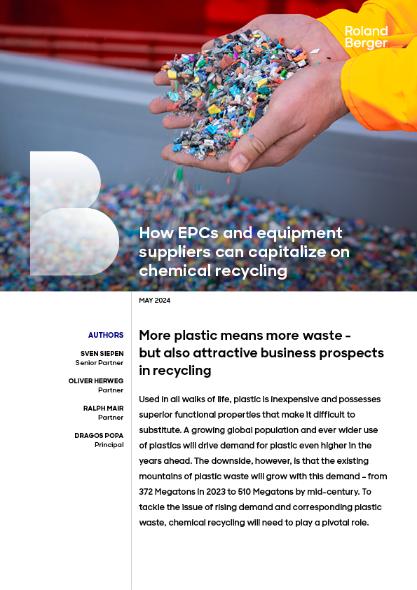
Moving mountains of plastic
By Sven Siepen, Oliver Herweg, Ralph Mair and Dragos Popa
How EPCs and equipment suppliers can capitalize on chemical recycling
Environmental problems associated with the use of plastic are an open secret. No one seriously disputes them. The dilemma is this: Plastic is so good at what it does that we keep producing more and more of it – a trend that is not about to change anytime soon. This being the case, recycling is one of the only realistic ways to tackle this serious sustainability issue. This, too, is no new insight. Yet even today, only just over a tenth of the world’s plastic ever gets recycled in practice.
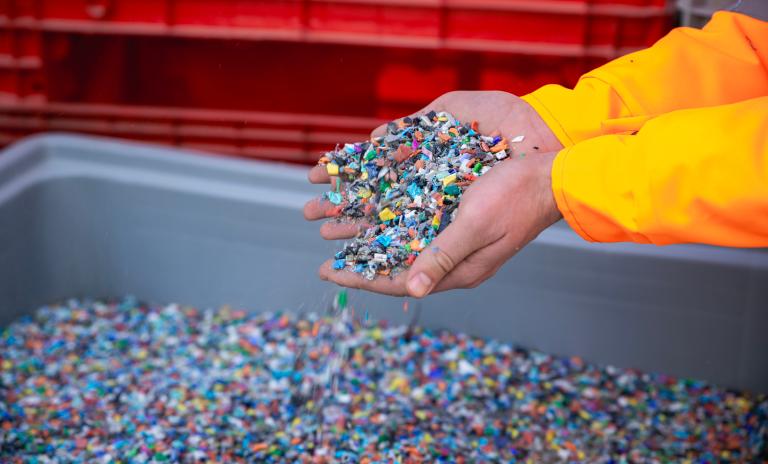
Our new study examines the key drivers of plastic waste recycling and the outlook for suppliers and manufacturers of the different recycling technologies. Specifically, it then homes in on attractive business opportunities that chemical recycling will open up going forward.
"Regardless of whether the EU opts for a fuel-exempt approach or a polymer-only mass balance approach, chemical recycling will unquestionably become an important and complementary plastics recycling technology."
After comparing the benefits and drawbacks of waste-to-x applications, mechanical recycling and chemical recycling, the report does the same for the different types of chemical recycling, each of which has its own strengths and weaknesses. Cost and quality issues are a key focus of the discussion, as are projected market developments and anticipated regulatory changes.
Based on thoroughly researched estimates of global capital expenditure for chemical recycling between now and 2050 (see the figure above), the report identifies extremely lucrative opportunities for engineering, procurement and construction firms (EPCs), but also for suppliers of key equipment who are bold enough to venture into this growing market space. In conclusion, market players’ current strategies are juxtaposed with the strategic issues that EPCs and suppliers must address now to position themselves for a profitable and sustainable future in the chemical recycling of plastics.
Register now to access the publication and discover how EPCs and equipment suppliers can capitalize on chemical recycling. Furthermore, you get regular news and updates directly in your inbox.