China's economy is undergoing a profound transformation. China has ceased to be the low-cost country with few regulations and a stable political environment. How should multinational companies react to the challenges that come with these instabilities? Should they reduce their footprint in China or leave the market altogether?


How German companies should reassess their China strategy
Adapting production and supply chains to the 'New China Story'
China is the world’s factory – producing 30% of the global manufacturing value add, sending the US to a distant second place with 18%. This includes a rising number of high-tech goods, produced in modern and highly automated factories. At the same time, supply chain obstructions and geopolitical incidents demonstrated the fragility of globalized value chains. Both developments force companies to reassess their business models to maintain their competitiveness, in the Chinese market and in their global network.
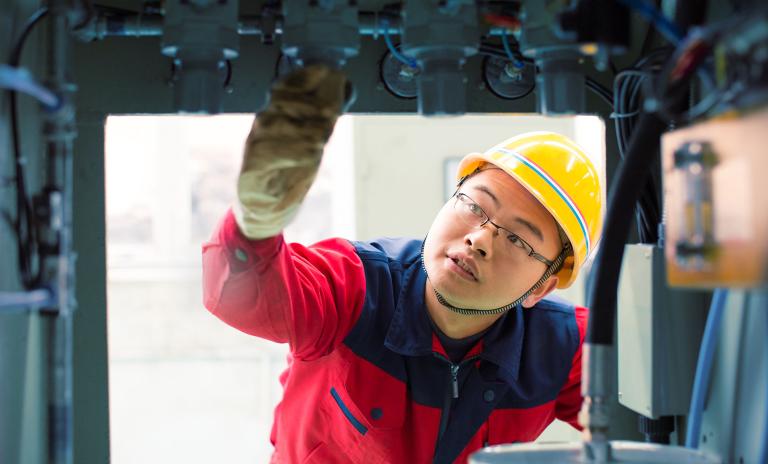
Re-evaluating the current China strategy is especially important for German manufacturing companies, as they can have a large interdependency with China, based on three factors: (a) Sales in China, (b) production in China and (c) (parts-)supply from China
- (a) China is Germany’s 4th largest export market, with exports totaling EUR 107 bn in 2022. Leading export industries are automotive, machinery, electronics, and chemicals. Companies such as Bosch, Schaeffler, Dürr, or Festo realize more than 15% of their revenue in China.
- (b) Around 5,000 German companies operate in China, and more than two-thirds of the German foreign direct investments in China went into manufacturing in 2022 – more than EUR 65 bn.
- (c) Global supply chains rely heavily on goods and parts manufactured in China. China is Germany’s largest supplier, with an import value of EUR 192 bn, representing 12% of 2022’s total imports. This includes commodities, machinery as well as critical resources, such as rare earth. Around 50% of 137 strategic essential products, identified by the Economist Intelligence Unit (EIU), are coming from China.
China’s transition towards a “New China Story”
China’s core manufacturing competitiveness in the past decades was mainly driven by low labor costs, loose environmental regulations, and high capital productivity. But China is changing, putting an end to the “Old China Story”. New features augment the “New China Story”, especially: (a) Industrial modernization, (b) low carbon emission development, and (c) rising demand from domestic consumption in China. We have analyzed the “New China Story” and its effect on multinational companies in detail: Link
While uncertainty and unpredictability of the future development of globalization have emerged, the fundamentals that made multinational companies successful in China remain. However, to stay competitive and accomplish a better engagement with the Chinese market, companies have to adapt their business models and mitigate risks according to the “New China Story”. So, how should manufacturing companies re-design their strategy around the new China story?
Finding the right strategy based on our dependency relation archetypes
First, every company needs to understand its own China dependency. How much revenue is generated in China, which production sites and assets are operated in China, and how large is the sourcing spend in China? What further parts of the supply chain have interactions with or in China? Depending on this rating, companies can group themselves into the following dependency archetypes.
If the current dependency is rated “very high”, companies can participate further in the rising domestic consumption of the Chinese market, and develop a China-for-China approach, resulting in our first archetype. This means relying on local production capabilities and a localized supply chain, for localized products, and processes, with local legal entities.
In case of a lower dependency on revenues in China but with Chinese production sites for the global or own domestic market, the “best-cost country production” archetypes can be applied. A potential step to mitigate risks and to continue benefiting from labor cost arbitrage is the regionalization or diversification of Asia, in a “China plus 1” or “China plus 2” strategy, investing in new “best-cost countries” in Southeast Asia such as Viet Nam, Thailand, or Malaysia while continuing production in China. It is not without risk, as the current productivity in these countries cannot compete with China’s output per worker yet, and large regional differences in the quality of infrastructure. Addressing these challenges by, e.g., on-the-job training or an improvement infrastructure, is critical as the Southeast Asian cost advantages are expected to shrink in the next decades as well. A potential alternative to Southeast Asia is a nearshoring approach, increasing production capacities in Eastern Europe or in Mexico to supply Europe and the US.
Aside from dependencies on the Chinese sales market and Chinese production sites, there is also a dependency on the purchasing of materials, parts or components, creating our 4th archetype of China being a supplier. Here, dual sourcing or targeted supplier changes can reduce dependencies and improve supply chain resilience. However, for a China-for-China archetype, a high sourcing dependency can also be interpreted positively by Chinese customers.
These simple high-level archetypes might give an indication for companies to re-think their China strategy and how to deal with the New China story in the coming years.
Our expectations for China as a production location
Many manufacturing companies are currently changing their global production footprint. 63% of the largest 100 machinery and equipment manufacturers made adjustments between 2018 and 2023, and 16% of the companies that adapted their production facilities did so in China. We assume this number will rise in the coming years, reacting to geopolitical shifts and challenges.
Foremost, we expect the “China plus 1” production strategy to gain momentum, strengthening the presence in the Chinese market while setting up more resilient supply chains. The strategy enables a true local-for-local approach to the Chinese market, increasing competitiveness and supply chain resilience.
As the China plus 1 strategy includes a production relocation, good preparation is essential for the movement, starting with a thorough scouting of the new production site (read more about NGM site selection criteria here). Capital investments should be analyzed towards flexibility, e.g., through so-called “hook machines” that can be transported easily for quick relocation. Knowledge has to be transferred for a smooth relocation execution, benefiting from a highly digitized infrastructure.
Our manufacturing and supply chain experts can re-assess and develop your strategy towards the new China story and help create a tailor-made solution for your company.
Register now to receive regular insights into our Operations topics.