The global construction equipment market is slowing down, particularly in North America, while the Chinese off-highway equipment market is seen as a focal point for analysis and planning due to its unique challenges and potential for growth.


Hydrogen – A promising fuel for off-highway equipment?
State of the art, comparison with electrification and future prospects for hydrogen-powered vehicles in construction and agriculture
To date, off-highway applications in disciplines such as construction and agriculture have generally been slow in moving towards zero-emission propulsion options. Unlike in other aspects of transportation, regulatory pressure has been uncharacteristically slack, so producers have been under little or no compulsion to invest heavily in developing viable zero-emission solutions.
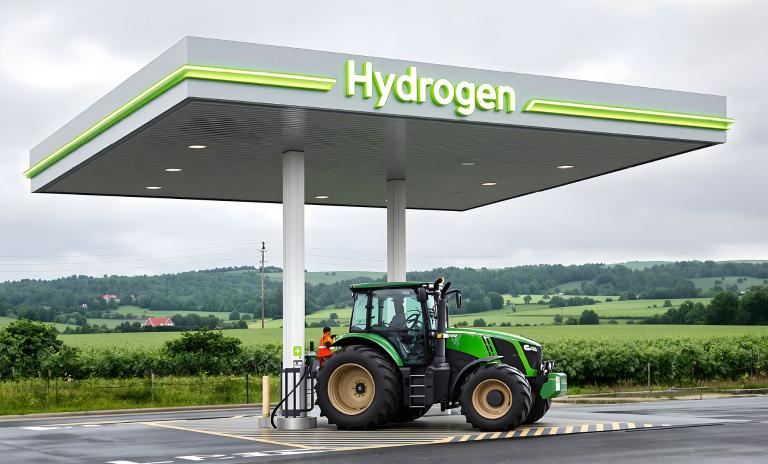
"If it is long periods of powerful operation that you are looking for – which is often the case for off-highway equipment – then hydrogen could become the lightweight fuel of choice."
Our new research nevertheless shows that this situation is now changing, for three main reasons: Regulatory pressure is mounting, as countries across the globe have now begun to implement emissions regulations for off-highway vehicles at both the national and local levels. At the same time, OEMs are seeking to fulfill sustainability pledges – and secure a strategic competitive advantage – by committing to the proactive development and launch of zero-emission models. In tandem with these developments, zero-emission technology is maturing increasingly. Significant progress has, for example, been made in battery electric and hydrogen fuel cell solutions for on-road uses, and these advances can now be adapted and leveraged for the off-road space as well. Between now and the arrival of fuel cell electric vehicle (FCEV) solutions that are generally viable, many OEMs see internal combustion engine-based (ICE) solutions burning hydrogen, synthetic fuels and biofuels as pragmatic interim approaches that can build on proven technologies.
As a result of these considerations and policy shifts, off-highway vehicle electrification is currently shifting up a gear, with large-scale roll-out already a reality in applications such as material handling. Going forward, the adoption of zero-emission technologies is expected to increase in off-highway applications through 2030. After a further decade – by 2040 – off-highway alternative propulsion solutions should reach penetration rates of 40 to 45%, albeit at different speeds in the construction and agriculture segments.
In the construction vehicle market, Western OEMs in particular are leading the charge towards electrification solutions for compact machinery upwards of 75 hp. Meanwhile, two alternative propulsion ecosystems are emerging in the agricultural space: While electrification is clearly the option of choice for on-the-farm applications, in-the-field applications are tending more towards biofuel and high-velocity oxygen (HVO) solutions, at least until FCEVs become an economically viable alternative. It is therefore worth taking a closer look at the comparative benefits and shortcomings of the various alternative propulsion technologies now under development.
Adapting conventional internal combustion engines to run on synthetic or biofuels is an obvious point of departure. Only minimal engine adaptation is required, keeping development costs to a low level. Perhaps even more importantly, such adapted engines can be retrofitted in existing off-highway vehicle fleets of all sizes – another powerful economic argument. On the downside, these solutions do still generate local emissions and thermal efficiency is poor. Worse, the fuel supply is inherently limited, and producing it requires the use of land that could otherwise be set aside for food production.
Battery electric solutions trump up with zero emissions, low noise, low maintenance requirements and comparatively high efficiency. Since grid capacity is often unable to power multiple large machines at once, however, these solutions are essentially only suitable for small to medium-sized vehicles, for which they require significant expansion to the charging infrastructure. Further disadvantages include low energy density, high battery costs and long charging times.
Looking at hydrogen, two different solutions – both of which can be used for medium-sized to large machinery – must be addressed separately.
- Hydrogen fuel cell electric (H₂ FCEV) technology harnesses an electrochemical reaction to generate electricity. The only byproducts from this reaction are water vapor and heat. There are therefore zero harmful emissions – neither greenhouse gases nor air pollutants – at the point of use. Very high energy density permits high power output and long operating periods. Maintenance requirements are low, and refueling (with a 10,000-psi tank) takes only about five minutes. On the other hand, the hydrogen used must be extremely pure, and these solutions are more expensive than ICEs. Also, since this solution is not yet mature, economic viability is not yet a given.
- By contrast, hydrogen internal combustion engine (H₂ ICE) technology works in a similar way to conventional gasoline engines. Here, hydrogen gas is burned instead of gasoline to generate mechanical energy. This technology can be implemented in hybrid systems with diesel used as a second fuel. It does have some issues with noise emissions and minor emissions of nitric oxide (NOx), however, and H₂ ICE technology is widely regarded more as a transitional technology until hydrogen fuel cells become more mature.
H₂ FCEV or H₂ ICE – Which will it be?
As things stand, it remains unclear which of these two alternatives will become the option of choice. Fuel cells have superior thermal efficiency in their favor, as well as true zero emissions (i.e. with not even the minor NOx emissions that hydrogen ICE solutions produce). However, fuel cells are currently more expensive due to low production volumes and the costly materials used, whereas ICE-based hydrogen solutions benefit from existing supply chain infrastructures and the experienced gained through conventional ICE research. These latter points in particular certainly make this a viable option as a transitional technology.
Many leading OEMs have already launched development projects for hydrogen-powered machinery based on both approaches. To date, the most promising use cases lie in heavy-duty applications, where hydrogen has convincing advantages (in terms of weight and charging times, for example) over electric solutions. Whichever option ultimately becomes established, hydrogen is definitely expected to play a tangible role in the decarbonization of off-highway equipment.
"The EU is tightening the regulatory screw in order to vastly reduce emissions. That is forcing OEMs in the direction of hydrogen – as an interim workaround, but also as a long-term solution."
Tighter emissions regulations across the globe
Countries around the world are currently pushing for stricter regulation of off-highway equipment emissions, with the European Union (EU) leading the way. It is expected that the EU’s Stage VI regulations will include limits on CO₂ emissions (as well as other kinds of pollutant emissions), but that they will not apply to off-highway vehicles (also referred to as non-road mobile machinery, or NRMM) until between 2025 and 2027. Proposals also exist to extend the EU’s Emissions Trading Scheme (ETS), which already covers emissions in the construction sector, to the transport sector as well. An even non-ETS sectors are under orders to cut carbon emissions by 30% by the end of the decade. Off-highway vehicles could likewise be affected by low-emission zones (LEZs) and zero-emission construction regulations in European cities by the end of 2025. In addition, many EU cities already impose noise restrictions of between 60 and 80 dB or even lower. Lastly, the EU’s Most Economical Alternative Tender (MEAT) guidelines for public procurement are also placing more and more emphasis on environmental considerations.
Across the Atlantic, the state of California is spearheading efforts to reduce CO₂ emissions in the USA. The California Air Resources Board (CARB) ban on internal combustion engines above 17 kW (24 hp) comes into effect this year, with 12 other US states currently expected to follow suit. California has also initiated a drive to push Tier 5 regulation that will further reduce permitted emissions thresholds, though this standard will likely not be introduced until around the end of the decade. Outside of the Sunshine State, however, most American cities have not yet progressed beyond debating noise emissions and construction noise. Nor are existing regulations widely enforced, with the result that no new measures are expected before 2030. The US government has nevertheless created financial incentives for retrofitting diesel engines and is currently being lobbied to include support for electrification in this program.
China has had Tier IV regulations (comparable to Stage V in the EU) in effect to curb nitric oxide (NOx) emissions and particulate matter since 2022. The country’s policy on preventing pollution and controlling non-road mobile machinery was ratified in 2018 and encourages the application of new energy technologies in the NRMM space. Also, cities such as Beijing and Shenzhen have begun to plan pilot projects to introduce zero-emission or near-zero-emission zones. For its part, Japan has introduced a number of overarching government strategies and policies, including a strategic roadmap for hydrogen and fuel cells. That said, no mention has yet been made of off-highway vehicles.
OEMs target net zero and a competitive edge
We mentioned earlier that equipment manufacturers are themselves also pushing the development of zero-emission models, largely to fulfill their sustainability pledges, but also to secure what they hope will be a strong competitive advantage. While most OEMs are focusing these efforts solely or primarily on electrification, some at least – in the EU, the USA and Asia – are exploring the future of hydrogen-powered off-highway machinery.
From a present perspective, however, the penetration rates that can be achieved by hydrogen as a fuel will ultimately depend on two factors alone: regulatory pressure and technological maturity, as illustrated in the chart below.
As the above chart shows, most growth in the hydrogen-powered off-highway machinery sector will come in the construction industry between now and 2030. Excavators and dump trucks are projected to achieve the highest penetration rates of 5% and 3% respectively within this timeframe. In this context, hydrogen can deliver long duty cycles, satisfies zero-emission construction site regulations and is perceived as “a green solution in a dirty industry”. Conversely, penetration in the agricultural vehicles segment will remain very low through the end of the decade.
Especially for OEMs looking to gain an edge in the transition to hydrogen-powered off-highway equipment, we see two topics in particular as crucially important at the present time: AI and product cost optimization.
As in so many industries, companies are gradually waking up to the reality of artificial intelligence (AI). However, many are still unsure about how this technology can best be harnessed to boost efficiency and performance in the context of product development. The use cases outlined above are literally only a few examples of what is now possible. Roland Berger has been involved in transformative AI projects from the technology’s earliest days. The wealth of experience we have gained can yield performance gains of around 25% for R&D budget optimization and cost savings, 40% lower prototyping costs and 60% shorter development cycles, to name but three examples.
We would welcome the opportunity to talk to you about the opportunities hydrogen presents for your future product portfolio, how we can help, and how your organization can reap the benefits of AI in the off-highway product development process.