" The shift to Industry 4.0 as a new paradigm is forcing a change in people's role in value chains. "


Man or Machine: Who is in charge of production?
- Industry 4.0 is an industrial ecosystem at the heart of which are intelligent software systems that enable highly-efficient and adaptive production through autonomous cyber-physical systems. The shift to this new paradigm is forcing a change in people's role in the industrial value chain.
Where today technical expertise, experience, human judgment and discretion are mandatory even for highly automated production processes, these skills will hardly add any value at the point of production in the real-time logic of future hyper-flexible production structures.
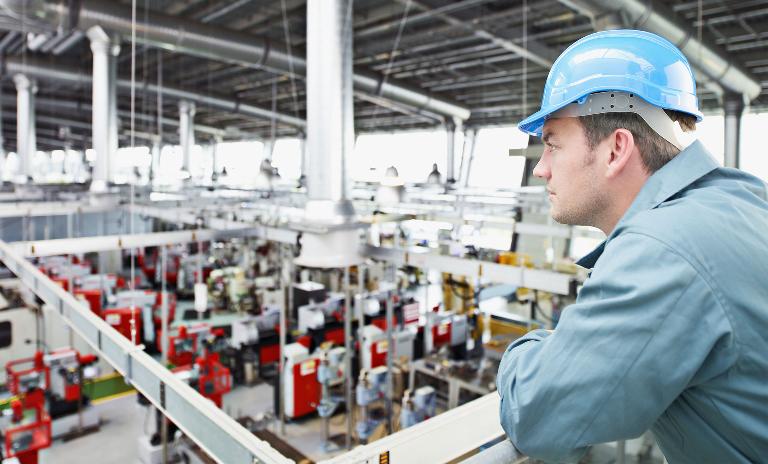
Let us not deceive ourselves: As with every wave of industrialization, Industry 4.0 will also destroy jobs over the long term. This time, however, it will be jobs that require experience – skilled labor and middle management positions – that the machines replace.
This is because expertise, practical experience and the ability to make sound operating decisions will be embedded in system logic itself. Sensory technology and self-teaching software will permit cyber-physical systems to increasingly improve their assessment of situations, learn from them and then independently optimize processes.
For all the risks it poses to the labor market, this also provides us with the opportunity to keep industrial value creation in Europe, despite a shortage of skilled professionals.
In a mature Industry 4.0 scenario, new professions and training concepts will emerge. System architects are the "brains" of Industry 4.0. They will combine traditional engineering skills with software excellence and the vision of a game designer. They will create a framework and rules under which the self-organization of production will take place.
Configurators and continuity engineers
Configurators will use intelligent interfaces to adjust systems to local conditions, but without needing to tackle the complexity of the processes. They are the users of the digital factory, who recognize errors and can adjust the parameters to the specific situation, but without having to exercise centralized control over the entire process in the traditional sense.
"For all the risks it poses to labor markets, Industry 4.0 also gives us the chance to keep industrial value creation in Europe."
Continuity engineers will be responsible for avoiding downtime and ensuring that value-adding processes don't stop, even if there are failures. They will provide ad-hoc solutions to minimize any damage from interconnected risks and combat the threat of cascade effects should any production stage crash. Operating decisions in Industry 4.0 will increasingly be made by the systems themselves, not only because of the complexity of data networking, but also to control risks.
If there are problems at a supplier, essential primary products can be automatically ordered from other providers using an industry platform. Production processes can then be kicked off there in real time. This will change relationships in the industrial ecosystem. Just like social networks have changed the social concept of friendship, relationships between companies in Industry 4.0 will be more diverse, looser and volatile.
Simultaneously, openness in terms of cross-company collaboration and the integration of data across processes will be necessary to actually realize value-creation potential. Significant spatial density and a diversity of industries, skills and company sizes provide the ideal setting for establishing such a highly flexible production system.
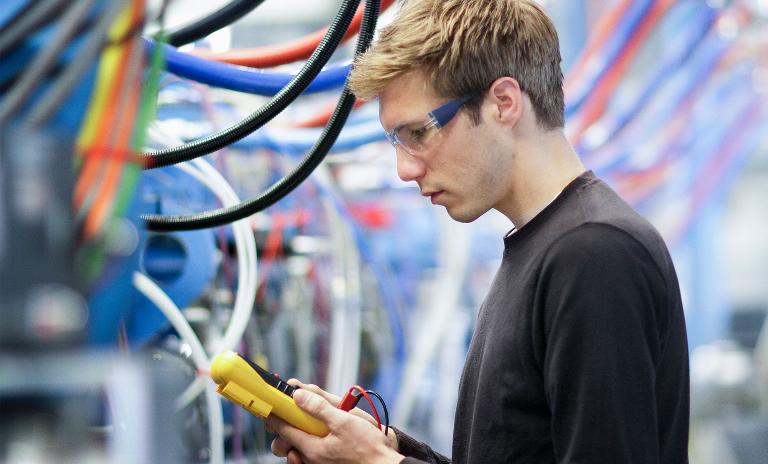
Cards will be reshuffled
From a global perspective, we can expect new production clusters to be formed not by industry homogeneity, but by virtue of adaptability and complementary competences in close physical proximity. The paradigm shift to Industry 4.0 means the cards will be reshuffled on all levels.
- Photo Credits: Sigrid Gombert / Getty Images; OJO_Images / iStockphoto