How to execute business strategy in India - More on Wilfried Aulbur's acclaimed new book here.


Manufacturing is cool: The reindustrialization of the triad
In the wake of the global financial crisis, Western nations rediscovered the charm of manufacturing as a driver of innovation, employment and services. The US, UK, France, and even Germany, which still has a healthy industrial base , all embarked on various initiatives to ensure manufacturing employment within their own national borders. Rather than going through all the initiatives currently underway, we will focus on "Industry 4.0", the German avatar of the reindustrialization drive.
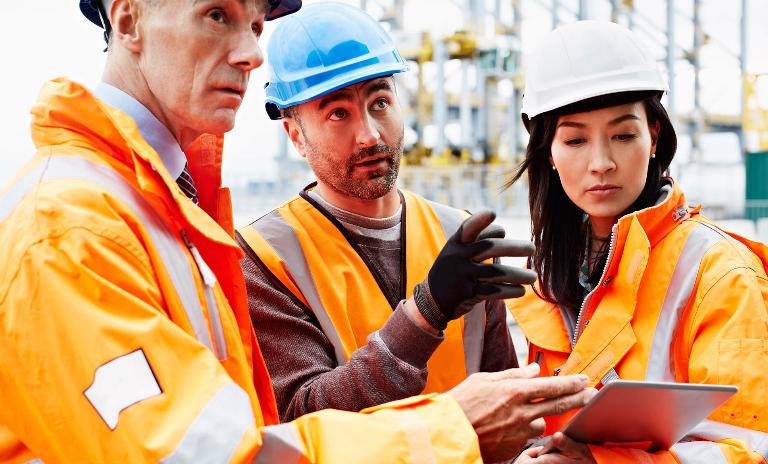
The basic premise of Industry 4.0 is that the introduction of intelligent machines, embedded cyber-physical sensors, collaborative technologies and networked processes will once again drive an efficiency revolution in industrial manufacturing. Industry 4.0 was initiated by the German Federal Ministry for Education and Research (BMBF) and officially launched with a report called "Securing the future of the German manufacturing industry" in 2013. Industry 4.0 aims to build the intelligent factory, which is characterized by adaptability, efficiency and full digital integration. Some components of this factory are smart robots and machines, i.e., multipurpose, "intelligent" robots that are able to adapt, communicate and interact with each other and with humans. Big data will be leveraged via cloud computing, e.g., for mass customization. Connectivity will reach a new level of quality via constant exchange of information between machines, work pieces, systems and human beings. Optimized production processes will ensure energy efficiency and allow for a decentralization of plants.
European companies in particular are positive regarding the potential of Industry 4.0. Expected cost savings of 14% on average over the next five years would negate a large part of the factor cost advantage that countries like India enjoy today vs. developed nations (typically in the range of 15-30%). Efficiency gains are expected to be even higher at 18% within the next five years. Industry 4.0 is a boardroom-level topic for all European manufacturing companies with investments in the approach amounting to 3.3% of revenues on average. In comparison, a typical R&D budget of Western automotive OEMs amounts to about 4-5% of revenue.
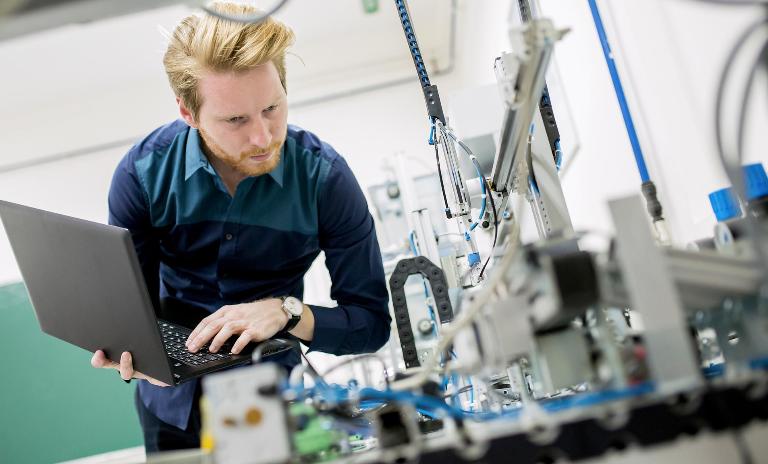
Established players in the EU are changing their organizations, processes and capabilities in whole or in part due to Industry 4.0. As freedom and flexibility of the production process increases, it will become possible to create products tailored for segment-of-one customer needs at relatively low marginal cost. Also, Triad distribution processes for spare parts or not too complex consumer goods may get easier, e.g., by leveraging 3D printing.
The value chain will be redefined. In a complex and intertwined manufacturing network, the roles of designers, physical product suppliers and the interfaces with customers will change. Supplier hierarchies and pecking orders are likely to be redefined. New companies (such as Amazon, Google and Apple) are increasingly integrating all parts of the value chain to enhance their core service offerings.
Last but not least, the need for offshoring work will reduce as will the number of available jobs in manufacturing overall. Take Baxter, the world's first general purpose production robot as an example. Baxter's base version costs only USD 25,000. It can be taught any task due to its learning capability and can work alongside humans due to a range of built in sensors. Baxter communicates with humans via a visual interface, and can recognize and dynamically adjust to work interruptions, wrong parts, etc. In light of these developments; India's "demographic dividend" could turn out to be a rather large "demographic liability."
The next Industrial Revolution is hence upon us, and like its predecessors it will lead to the introduction of new products and of new means of producing existing ones. It will disrupt the competitive status quo, on a company, country and or regional level, and drive new requirements for workforce and infrastructure alike. Unfortunately, India's automation and digitalization levels are not adequate.
Opportunities to leverage the country's pool of well-trained engineers and IT professionals in order to drive an Indian version of Industry 4.0 clearly exist and should be pursued with the necessary effort and investments. While Industry 4.0 contains risks, automation and productivity enhancements are likely to be the recipe to ensure increasing livings standards for Indians and to build a tax base that can finance inclusive growth.