MedTech saw profit dip in 2022-23; European firms hit by supply chain disruptions, rising costs, and inflation. To recover, prioritize operational excellence, embrace ESG for long-term viability.


Operational excellence benchmarking: Shaping the future of MedTech
By Thilo Kaltenbach, Marco Bühren and Stephan Fath
Our first-in-industry tool enables MedTech firms to create data-driven operational strategies
The MedTech sector is facing growing cost pressure, making operational excellence (OPEX) more important than ever. Benchmarking is a vital part of this: Do you know how your company compares against competitors? What are the gaps between your firm’s performance and that of industry leaders, and what levers can you pull to improve results?
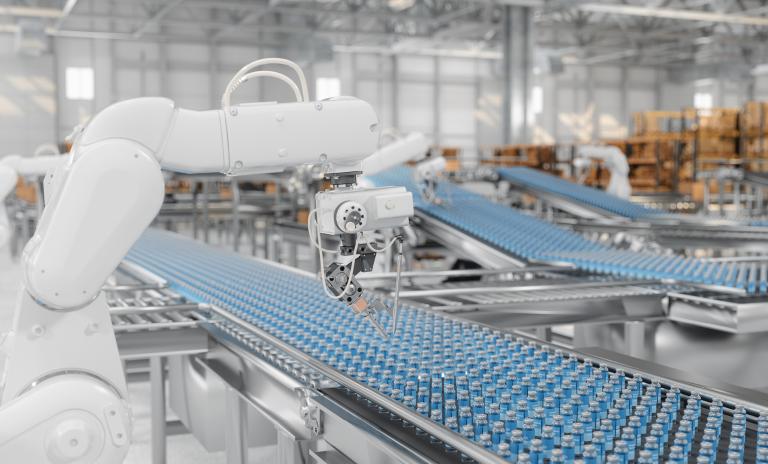
"Roland Berger and the University of St.Gallen have developed the world’s first dedicated MedTech OPEX benchmarking tool."
These can be difficult questions to answer. But now, Roland Berger and the University of St.Gallen have developed the world’s first dedicated MedTech OPEX benchmarking tool to help boost your company’s competitive edge and achieve lasting improvements.
Fully assess OPEX across an organization
Our MedTech OPEX benchmarking tool combines industrial data with science-based practices, principles, and philosophies to fully assess OPEX across an entire organization (see infographic). It has an end-to-end focus across each manufacturing site, while also covering network and corporate aspects. There are three main levels of information:
- Key performance indicators: Hard facts and outcome metrics to determine the performance of your organization.
- Implementation of leading tools and approaches: Assess the maturity of your organization to see if performance is built on solid foundations; discover which levers to pull to improve performance.
- Structural factors: A variety of contextual factors provide greater detail and enable more meaningful comparisons.
The benefits of MedTech OPEX benchmarking
Our MedTech OPEX benchmarking tool offers numerous benefits:
- Obtain a data-driven, scientifically proven external perspective
- Receive a holistic overview of your company’s strengths and weaknesses
- Make meaningful comparisons to real high performers
- Derive the right implications to make improvements with measurable and sustainable impact
"MedTech OPEX benchmarking enables meaningful comparisons to real high performers."
Once you have completed the MedTech OPEX benchmarking, your business will receive an individual report per participating site. Each report comprises an extensive performance review, in-depth maturity assessment, and many more structural factors to clearly show the full picture. High performers and peer-group median benchmarking values show where your organization stands within the industry and your closest peers.
Additional activities, such as an implications and measure workshop, can be arranged upon agreement.
You can start benchmarking at any time, across as many sites as required. The initial questionnaire is Excel-based, ensuring easy management across your organization. While you and your on-site staff gather the data, Roland Berger and the University of St.Gallen team provide remote support. An outline of the process is shown below.
"This unique benchmarking tool allows to benchmark performance in a contextual environment, making sure to compare apples with apples."
How we honed a precise benchmarking tool
It took a year for Roland Berger, the University of St.Gallen and a selected group of industry peers to develop the benchmark. Building on the foundation of St.Gallen’s renowned pharma OPEX benchmarking, we have gathered extensive information in workshops and interviews with MedTech companies and experts. We then jointly developed the questionnaire, honing the benchmarking into a precise tool to deliver meaningful insights to MedTech companies.
Further information
If you’d like to know more about the unique MedTech OPEX benchmark, please contact the authors.
The FAQ section below also answers some of the most common questions.
FAQs