

Rethinking Global Automotive Production Networks
Current trends and conflicts call for a transformation of automotive production networks
Rising logistics costs, trade conflicts and the pandemic have left the global automobile manufacturing model exposed. In this special report, Roland Berger examines the best road forward for international automotive players.
Management Summary
To serve global markets, vehicle manufacturers pooled production volumes to achieve economies of scale but lost sight of regional dependencies and even neglected transregional transportation services. The coronavirus pandemic has mercilessly exposed the vulnerability of global production and sourcing structures in the automotive industry . Inadequate supply capabilities in weakening regions led to severe disruption in the economies of dependent regions.
The short-term consequences of the pandemic – namely a collapse in demand and the negative effect of temporary border closures on international supply flows – have put automobile makers under significant financial pressure. But the pandemic doesn't shoulder all the blame. Rising logistics costs, increased carbon taxes and intensified trade conflicts are also challenging existing production and procurement structures.
Demand structures for vehicles are shifting enormously in some cases, presenting manufacturers with major challenges. For example, Full-size SUV production is mainly located in North America and Europe, while demand for this segment has risen sharply in Asia in particular. The only way for vehicle manufacturers to cope with this lately has been through higher transportation costs and challenging supply adjustments.
In our view, manufacturers need to reorganize their production and sourcing in a way that production and sourcing structures better match regional demand to achieve a holistic cost optimum. Increasing production flexibility , regionalized manufacturing and risk management are appropriate levers to deal with the uncertainty arising from trade conflicts, rising transportation costs and border closures.
Thus, automotive manufacturers can emerge stronger from recent conflicts and in better financial health with new risk profiles and novel supply strategies. By simplifying, shortening and regionalizing their value chains with more agile, digital and innovative technology, adaptive manufacturers will secure their futures.
"To counter numerous global issues and megatrends disrupting the automotive industry, manufacturers must increase resilience and agility by thinking globally but acting regionally."
Setting the scene
In recent years, most automobile manufacturers have pushed for greater globalization, which has resulted in more global value creation structures. But with greater globalization came more complexity by way of wide-ranging production and supply chain networks that are often difficult to manage when responding to regional or local demand.
To bundle production quantities, some vehicle models are produced at one location and then sold all over the world at considerable logistical effort. Meanwhile, however, the demand structures have shifted enormously, most notably in the case of Asian appetites for large SUVs, whereas the production capacities have remained in North America and/or Europe.
Obviously, the general economic downturn caused by Covid-19 became an even greater disruptive factor that exerted considerable financial pressure on automakers. But the globalized conflicts of the past 20 years have been increasingly linked with an ongoing decline in both economic power and customer purchasing power.
Yet Covid-19 caused another significant consequence: the temporary closure of important production facilities and the interruption of cross-border supply flows. In light of this, global manufacturing has become extremely vulnerable. This, in turn, leaves global supply chains exposed. And indeed, global automobile production proved too fragile to meet the needs of a temporarily deglobalized market.
In the future, these findings must be taken into account when redesigning production networks and supply chains to mitigate the vulnerabilities and consequences of global value creation. Although it was understandable in the past to want to source globally to serve an increasingly globalized market, the pandemic shed light on the opportunity for regionalized production as a way to manage ongoing conflicts, however sustained or lasting they may be.
Although regionalized production wouldn't have prevented the global economic downturn caused by the coronavirus outbreaks, it could have lessened the blow of cross-border supply closures, regional changes in demand and tariff tensions had it already been in place.
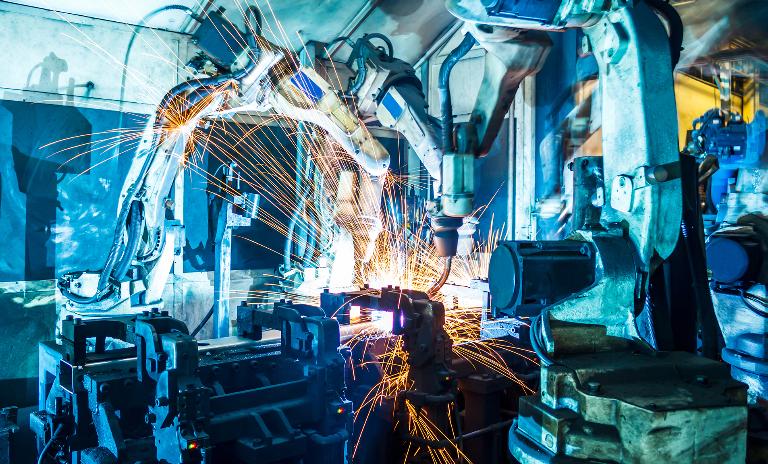
Future trends
As we've previously reported, there are four trends that are changing not just the automotive industry, but the entire mobility ecosystem. They include: Mobile innovation, Autonomous technologies, Digital features and Electric vehicles (or "MADE") . After extensively studying, researching and analyzing the industry, we at Roland Berger believe these four megatrends will likely trigger a major disruption within the next 10 to 15 years.
But there are other influences at work, of course, especially for automotive manufacturers. In addition to combating disruptions brought about through the MADE trends, the automotive industry must also contend with three overarching megatrends that will impact the supply, sustainability and politics of the global automobile market.
These are as follows:
- Technology: A new industrial revolution is taking place. As advanced robotics (i.e. industrial automation ) and artificial intelligence (i.e. "white collar" bots) proliferate, the automotive industry must consider the ramifications and opportunities of these technologies. Furthermore, automakers must prepare and plan for continued digitalization of supply chains through cloud platforms and internet-connected sensors, as well as how 3D printing might further revolutionize the industry.
- Policy and economic governance: In terms of political governance, there are three growing social trends that will likely influence the future of automobile production in some form. Accordingly, each must be accurately assessed and considered: 1. More interventionism in national policies, including industrial, competition and fiscal policies 2. More protectionism in trade and investment, including tariffs and non-tariff barriers, as well as the potential impacts of trade wars 3. More regional, bilateral and ad hoc economic cooperation, such as favorable trade deals among selected groups
- Sustainability: Since the turn of the century, the desire for energy and environmental sustainability has only grown. It has changed how nations and societies enact "green" policies, including both regulations and carbon adjustments. It has also resulted in reputational and market-driven changes, including demand for sustainable products. And it has impacted supply chains, their resilience and how they source both goods and services around the world.
In short, these three megatrends demand technological progress. At the same time, they must be used to ensure ongoing political interests and eventual sustainability.
Production scenarios
The regional demand structure for vehicles has undeniably changed in recent years. But the manufacturing network structures have not changed with it. Consequently, this has led to a rise in logistical costs, inflexibility and even sustainability challenges. As previously emphasized, trade conflicts, a rise in transportation costs and the pandemic have all exposed the vulnerabilities of the global manufacturing structure.
"It's time for change. It is now clear that innovative product design and production methods from the "new kids on the block" have the potential to significantly disrupt the market. By using modular cell production and the latest manufacturing technology, such solutions are cost-effective even in smaller volumes."
To get a sense of the current climate, a few pertinent statistics can help: European suppliers have increased exports of vehicle parts enormously during the last 15 years. Germany today accounts for 15% of total global exports of vehicle parts. Eastern Europe's share is growing. North America has largely lost its global trade share to Asia. Mexico is emerging as the preferred low-cost supplier. And within Asia, China and South Korea have taken significant export share from Japan, especially since 2010.
Against this backdrop, growing logistical costs, both inbound and outbound, and increasing sustainability requirements will demand a full review and reorganization of global manufacturing structures. Given current trends and rising uncertainty, logistics providers have already increased their prices. Therefore, most global automotive companies face a significant and continued rise in transglobal transportation costs. This is a major burden for most OEMs and their suppliers.
Consequently, targeted regional sourcing will become more important in the coming years as an overriding lever for sustainable cost reduction. This will require the regional establishment and development of high-volume suppliers, volume discounts through regional value creation, and backup facilities that are as close as possible to the regional manufacturers' factories.
On top of that, automakers must compete with a deluge of new and even well-established mobility technologies such as the "last mile" personal transportation vehicles that have recently commoditized car ownership. This puts traditional players under enormous pressure to adapt and renew their approach for their rightful place in the changing automotive landscape. It will ultimately require additional investments that are removed from the traditional manufacturing process, in addition to shedding outdated resources that no longer contribute to the bottom line. These new technologies are exerting additional pressure on the players in the automotive industry. Adhering to traditional processes or making selective changes will not suffice in this new normal. That's why automakers need to address change comprehensively and radically.
Crucial criteria
In order to counter existing challenges and achieve the above results, a number of essential perspectives and questions must be answered convincingly and agreed upon by all relevant decision-makers. These are as follows:
- Demand: How high is local demand and how does variance affect certain regions?
- Product: Which product mix best satisfies the targeted demand of each regional market?
- Production volumes: How must regional volumes be reallocated and how can production flexibility be increased?
- Sourcing: How can regional material supplies be ensured, and interdependencies reduced?
- EV share: What additional manufacturing and logistical requirements are needed to increase our share of rising electric vehicle demand?
- Risk management: How can we manage future cross-border closures and their impact on global and regional supply flows?
In our view, tomorrow's leading automobile manufacturers will structure their global manufacturing and supply chains with the following premises in mind:
- Regionalized production networks ("build where you sell")
- Regional supply chain networks ("source where you build")
- Regional warehouse and reserve strategies ("store where you sell")
- Reduction of variants and focus on radical increase in efficiency ("reduce complexity")
- Establishment of sustainable risk management ("master the volatility")
When coupled with the rise of several megatrends, a successful transformation of global production networks necessitates the six skills (or key criteria) in the following graphic: competency assurance, digitalization, agile collaborations, production elasticity, and both economic and ecological sustainability. Whether completed internally or with the help of an experienced external advisor, these criteria must be met to ensure that production structures are fit for the future.
Of course, there are other factors that must be considered. These primarily include the political climate, global trade tensions and pandemic shocks. But they also include product design, which must equally shift from the traditional global centers to more regional ones that are better based upon local consumer tastes. To achieve this, regions must operate more independently of each other.
For example, vehicles today are still produced on a large scale at single locations and then delivered to sales markets. The traditional assembly line approach from 100 years ago is still in use today and sets the framework for efficient plant dimensions. But with a view to more flexible production networks, new concepts need to be implemented. New startups in the EV sector are currently investing in disruptive manufacturing concepts that enable efficient small-scale manufacturing on a more regional footprint. That reality should serve as a wake-up call, if not immediate inspiration, for automotive manufacturers.
Lastly, we believe agile collaborations with other manufacturers might enable the joint use of regional production capacities to help alleviate global production limitations and any regional-related risks and challenges. Even if some of these concepts fail, the message is clear: simplifying, shortening and regionalizing manufacturing supply chains is the most appropriate response to automotive deglobalization conflicts.
Conclusion
Automotive "glocalization" is both real and justified in light of recent conflicts, namely trade tensions, rising logistics costs and prolonged border closures and market disruptions brought about by a global pandemic (or any other future disruptions to cross-border trade). To successfully navigate this transformation, automotive manufacturers, their suppliers and the industry as a whole must regionalize their production structures.
In very concrete terms, the interdependencies between production and the supply chain must be thought through in order to counteract rising logistical costs and the risk of delivery failures. To achieve this, respective regions must act more independently of each other. The motto must therefore become "region for region" or "build where you sell".
Naturally, our proposed solution concepts have to be adapted to the specific manufacturer and depend, among other things, on the value-added structure and on the specific product configuration. But fundamentally, a rethinking of today's global production and supply structures is absolutely necessary. Automotive production must become more regional in the future.
But this is only one side of the equation. A successful transformation of global production networks, a breaking away from the previous order criteria and a willingness to manufacture in new ways (including cooperation with other manufacturers) are all on the other side of the balance. As you navigate this strategic transformation, we hope you'll consider Roland Berger as a qualified and experienced partner.