Expert jury members for the Microsoft Intelligent Manufacturing Award.
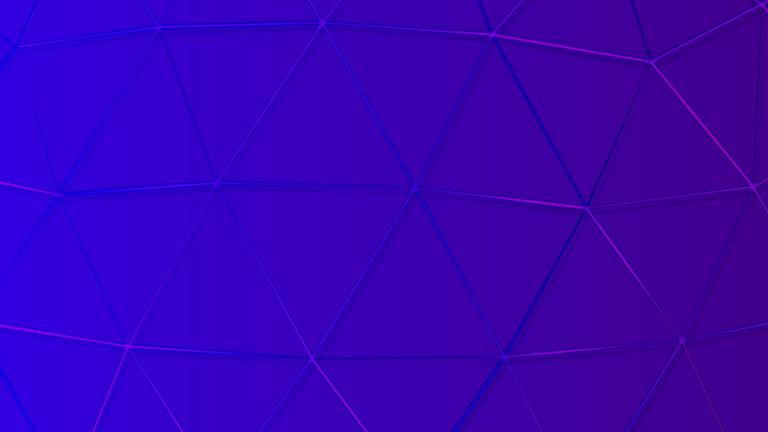
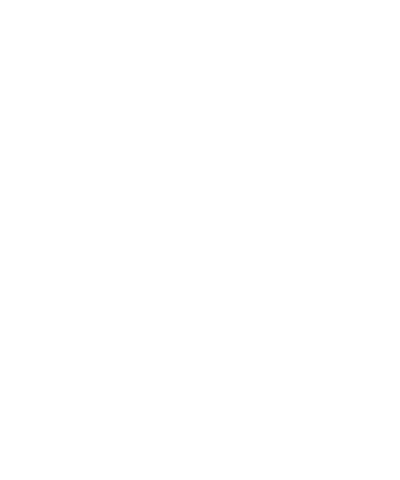
AWARD
The winners of the Microsoft Intelligent Manufacturing Award 2025
Roland Berger and Microsoft honor digital innovators in Operations
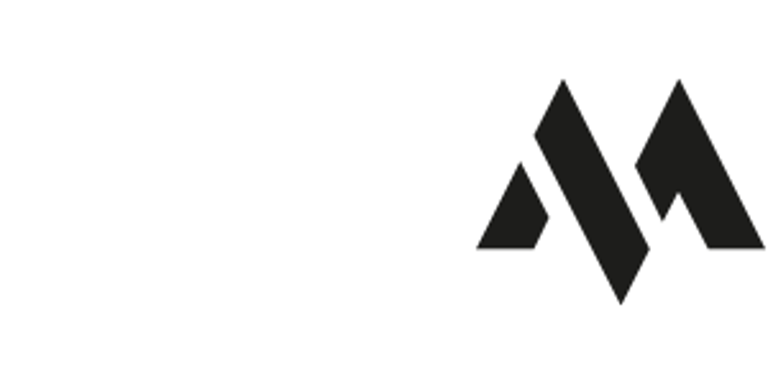
For the sixth time, Microsoft Germany and Roland Berger have recognized pioneering solutions for the manufacturing industry with the Microsoft Intelligent Manufacturing Award (MIMA). The competition invited industrial companies from Europe, the Middle
East and Africa to submit digital solutions for the manufacturing, process, construction and automotive industries. Following the first selection round, 13 finalists had the chance to pitch their projects to a high-profile jury. The six award-winning projects aren’t just innovative but, according to the jury, also have the potential to drive digital change in the entire sector.
"In this year’s MIMA, we saw an impressive increase in digitalization maturity. The winning solutions truly embody the MIMA 2025 motto of ‘Accelerating future operations’ by boosting the tremendous efficiency and value-add potentials, which were previously only aspirational goals."
Jochen Gleisberg, Partner at Roland Berger and member of the expert jury, praised the award winners on their achievements: "Once again, we have seen just how creative and innovative some manufacturing companies can be in striving for operational excellence. Their solutions showcase an incredible dedication and commitment to accelerating future operations.
According to Paul Röhrs, Director Industry Advisor for Manufacturing and Mobility at Microsoft Germany, "The future of manufacturing will be shaped by smart data usage and the collaboration of workforce and AI-powered copilots. The Microsoft Intelligent Manufacturing Award recognizes the most outstanding solutions driving this transformation. This year's winners exemplify the innovative application of next-generation technology to surpass traditional efficiency boundaries, achieving superior quality at reduced costs while enhancing sustainability. The MIMA celebrates this dedication and sheds a light onto continued advancements in the digital transformation of the manufacturing industry.”
Applicants for the MIMA 2025 were able to demonstrate their innovative excellence in five categories: Innovate!, Scale!, Add Value!, Disrupt! and Sustainability! The MIMA jury then selected one winner in each category as well as the overall winner.
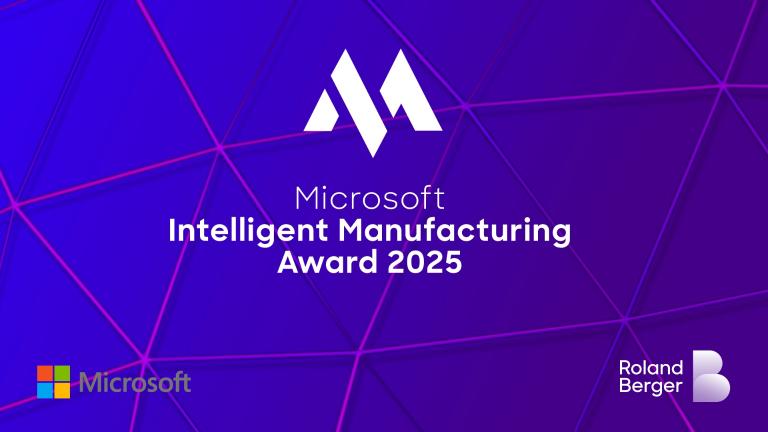
MIMA 2025 Finalists
In addition to the six winning companies, eight other finalists from this year's competition will enter the exclusive MIMA Champions Circle:
- Bosch: “Hey Bosch” – Interactive 3D agents, enriching end-customer training and support
- Aira & MTEK Industry: Revolutionizing residential heating manufacturing with MBrain
- Schneider Electric: GenAI-based PLC code generation for 61131
- E.ON Grid Solutions: Transformation of E.ON's Meter2Cash business through the SPACE IT program
- Sandvik: Manufacturing copilot
- VERIFI / Saint-Gobain: Innovative concrete management with Verifi, enhancing efficiency and sustainability
- Kongsberg Digital: The AI-powered digital twin
Together with the winners of MIMA 2025, these eight finalists will become part of an exclusive networking platform for technology leaders in the manufacturing industry, consisting of all finalists from previous years.