ローランド・ベルガーは、Next Generation Manufacturing(次世代製造業)への転換を志向するメーカーをご支援するため、未来志向のコンサルティング・サービスを幅広く提供しています。

_download_preview.jpg)
「インダストリー4.0」はどうなったのか
デジタル・マニュファクチャリングを先導する自動車企業 — 他産業は何を学ぶべきか
「インダストリー4.0」―製造工程のデジタル化がもたらすであろう飛躍的進歩を言い表すこのコンセプトは、10年以上前にドイツで生まれ、以来長い道のりを辿ってきた。現在、多くの面で自動車業界が先導している。ローランド・ベルガーは、喧伝と現実とを区別するべく、世界の大手自動車OEM、一次サプライヤー、その他の業界専門家に対して綿密なインタビューを行った。本記事は、その包括的なレポートを要約したものであり、自動車業界のこれまでの「インダストリー4.0」への取り組みから他業界が学ぶべき貴重な教訓のエッセンスを抜き出したものである。
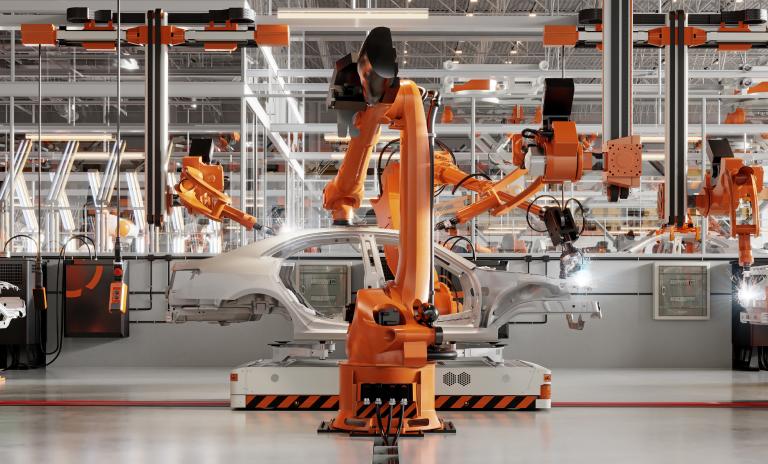
「As different processes and/or technologies in automotive production are more or less suitable for digitalization, weighing up how much added value can actually be created is a very important factor for each individual use case.」
製造デジタル化の10年
10年ほど前、中でも(ドイツの)自動車業界は、デジタル・マニュファクチャリングのユースケースの特定、開発、導入に多額の投資を始めた。ところが当初の興奮が収まってみると、時代遅れでばらばらの業務・情報基盤、デジタル化がもたらす効果の定量化(ひいては、投資家の説得)の難しさ、適切で有能な社員の再教育・採用など、数々の技術的・組織的課題が明らかになってきた。また、企業内のタコつぼ思考が、デジタル化に必要な部門間協力の前に立ちはだかることも少なくなかった。
それから10年以上が経ったが、自律的で柔軟性が高く自己組織化する工場という当初のビジョンの実現は、いまだ遠い先の話である。そこで「インダストリー4.0」の現状を正しく把握すべく、ローランド・ベルガーは詳細調査を実施、実際に何が実現し、何が実現していないのかを追跡した。具体的には、自動車業界が重点的に取り組んだユースケース、その進捗度、OEM、OES、あるいは地域ごとの違いを分析した。また、各ユースケースが実際にどのように開発・実施され、どのような組織変更が必要であったのかも併せて調査した。
自動車業界は、現在「インダストリー4.0」を何に利用しているのか
ローランド・ベルガーは、自動車産業における7つの主要ユースケースの「型」を特定、中でも5つの特定ユースケースに着目した。すなわち、機械パラメーターのリアルタイム最適化、状態監視と予知保全、外観/プロセスデータに基づく自動検査、イントラロジスティクスにおける自律的マテリアル・ハンドリング、サプライチェーン上の輸送追跡の5つである。
「The number of use cases for cobots with a positive business scenario is limited. Cobots are mostly only suitable for post-automation of workstations that were originally designed for manual work.」
上記リストに協調ロボットが含まれていないが、これもまた興味深い発見である。当初「インダストリー4.0」の可能性が様々に喧伝されたが、検討が進むにつれ、投資対効果があると判断された協調ロボットのユースケースは限定的であることが明かになった。現在、協調ロボットが利用されているのは、もともと手作業用に設計された生産ラインの自動化後であることが多い。
自動車生産で使用される様々な工程や技術は、デジタル化適合度もそれぞれ異なる。他産業でも間違いなく同じことが言え、個別ユースケースがデジタル化によってどれだけ真の付加価値を創出するかを正しく評価することが非常に重要となる。そこで、ローランド・ベルガーは、OEMやOESが使用する製造工程を詳しく調べるとともに、例えば、国によるコスト競争力の比較優位が、企業のデジタル化の優先度に及ぼす影響を分析した。自動車企業における優先度の高い5つのユースケースは、デジタル化のメリットと課題を浮き彫りにしている。以下はその概要だが、レポート本編には詳しい説明が掲載されている。
- 状態監視と予知保全
予知保全は、稼働率向上と設備総合効率(OEE)改善が期待できることから、明らかに検討する価値のある選択肢であるが、実導入に当たっては、既存システムへの組み入れ費用の高さ、自動車企業に深く根付く固定化した保守スケジュールなど、いくつかの課題に直面することがある。そのため、現時点で実際に導入されているのは、比較的単純な予知保全アプリケーション(モーター電流解析など)に限られている。全システムを対象とする複雑なユースケース(産業用ロボットなど)は、今も開発途上にある。これらの課題にもかかわらず、特に部品製造用のCNCマシニングセンターや車体工場の産業用ロボットなど大規模システムに導入された場合に予知保全がもたらす大きな価値と、これまでに投資された資源量を踏まえると、予知保全のユースケース数は、今後急激に増加すると予想される。 - 品質検査の自動化
プロセスデータやセンサーデータを利用すれば、そのデータの異常を特定することで、品質問題の可能性を検知・予測できる。また、抜き取り検査に代わってデータに基づく検査を導入すると、より早い段階で品質検査を行ったり、数や精度を増やすこともできる。外観検査とプロセスデータに基づく検査との間には、次のような違いがある。
注目すべきは、単一部品の外観検査、インライン検査、早期検査である。外観品質検査は、機械学習の一種である深層学習が著しく進歩した結果、かなりの付加価値をもたらしている。テクノロジーは概して相当成熟しており、時間をかけずに即導入できる。それでも、実際のユースケースの大半はまだ初期段階/試験導入段階、あるいは開発段階にある。今後数年内に、安価なカメラと複雑な機械学習モデルを組み合わせて利用できるようになれば、より広範な導入が加速するだろう。
プロセスデータに基づく検査も、シンプルなアプリケーション(ねじ付き部品の品質チェックなど)が最も導入しやすく、多くのモデルやプロセス制御が既に提供されている。プロセスやパラメーターを十分に理解した上で、シンプルな統計モデルと組み合わせて用いれば、確実に実効性が得られる。しかし全体的には、プロセスデータに基づく検査は外観検査ほど成熟していない。実現済みのもの以外にも、より複雑な検査方法の研究が進められている。 - 機械パラメーターのリアルタイム最適化
機械パラメーターの設定を行うことができるプロセスの専門家は、数が少なく人件費も高いため、その部分を自動化するという考え方は明らかに魅力的である。そのため、自動最適化は、クリーンルーム管理などのプロセス・パラメーター整に既に用いられている。この分野もやはり、導入済み領域は、理解の進んだプロセスのパラメーターの一部を対象にした非常に基本的なユースケースである。ここには多くの課題があり、より複雑なユースケースが今後10年内に実用化される可能性は低い。当面、自動車業界における機械パラメーターの最適化は、プロセス専門家の意思決定支援を目的とする情報入力に限定されると考えられる。 - イントラロジスティクスにおける自律的マテリアル・ハンドリング
大幅なコスト削減の可能性があるため、自動車企業ではこの種のアプリケーションの優先順位が高い。直接の搬送作業は既に大部分が自動化されているが、その補完として、間接的にマテリアル・ハンドリングの自動化を行えば、生産現場の人件費やエラー/廃棄物を大幅に削減できるはずである。しかし、物体の形状や人間と共有する作業空間のばらつきに起因する問題は未だ完全には解決されておらず、大型重量物の自律搬送は、まだ完全には実用化されていない。一方で、小型軽量の比較的重要ではない部品の無人搬送は導入済みで、倉庫と組立ライン間の輸送や出荷物流領域でも問題なく機能している。 - サプライチェーン上の輸送追跡
当初は、重要部品の購買物流領域に焦点を当てて初期課題の克服に取り組んでいたが、今では、一部OEMは出荷物流領域にも適用し始め、完成車両の出荷追跡を行いつつある。生産停止によって莫大なコストが発生する状況ではリアルタイム自動追跡が極めて重要で、多くの自動車企業がこのユースケースの実現を待ち望んでいる。
自動車業界はどのように開発・導入を推進しているのか
ローランド・ベルガーは、前述の多くの課題や障壁への対処方法について、自動車業界のリーダーや専門家に話を聞いた。その結果、ふたつの主要分野で類似のパターンや傾向が明らかになっている。ひとつが組織構造・運用モデル、もうひとつがIT/OT(情報技術/運用技術)アーキテクチャーである。
- 組織構造・運用モデル
従来型の製造工場は互いに独立しているため、機能重複や不整合が生じる。それを克服すべく、デジタル化に熱心な大手OEMはとりわけ、ハブ・アンド・スポーク型組織を好む傾向にある。主としてユースケース主導のアプローチを採用し、「ハブ」(中央拠点)で必要なデジタルスキルや生産スキルを蓄積し、「スポーク」(他の分散生産拠点)と緊密に連携を図る。また、大半の企業が魅力的なユースケースを特定し、その優先順位を決め、プロトタイプ開発し、パイロット運用を行い、生産ネットワーク全体に導入する、という5ステップからなるモデルを運用している。ローランド・ベルガーのレポート本編では、このモデルを効率的に機能させるために「ハブ」と「スポーク」間に求められるコミュニケーションや協力方法を詳細に分析している。
- IT/OTアーキテクチャー
包括的なIT/OTアーキテクチャーは、ユースケースを一つずつ展開していく際に生じやすい冗長性やミスマッチの回避に役立つ。これらのアーキテクチャーには標準化と相互運用性が最初から組み込まれているため、新たなユースケースを迅速かつ効率的に、また一貫性を保って導入できる。ドイツを代表するOEMは、一次サプライヤーをアーキテクチャー内に組み入れる取り組みを開始しているが、OESは現在のところ、社内調整に重点を置いている。
他の産業は、自動車業界の取り組みから、何を学ぶことができるのか
デジタル・マニュファクチャリング分野でこれまで自動車企業が行ってきた、また現在も行っている先駆的な取り組みから、幅広い産業が貴重な教訓を学ぶことができる。ローランド・ベルガーは「インダストリー4.0」を他セクターに取り入れたいと考える企業に向け、詳細な分析結果から4つの実践的提言を抽出している。
- ユースケースとリソースの優先順位付け
コスト削減、品質向上、エネルギー節減など、様々な面で得られる付加価値を定量化することで、企業は最大の利益回収が見込めるユースケースを特定し、そこに注力できる。投資対効果は経済環境や地域要因によって当然異なるが、説得力ある事業計画は定量化あってこそ、である。 - ハブ・アンド・スポーク型組織の編成
中央拠点(「ハブ」)は、データ分析やその他の生産・IT関連の能力と、他の分散生産拠点(「スポーク」)に変化を導入する権限とを併せ持つ必要がある。逆に、各工場は中央拠点が行うことを積極的に支持する必要があり、透明性が高く、説得力ある双方向コミュニケーションが不可欠になる。加えて、デジタル・マニュファクチャリング部門がもたらす付加価値は、誰の目にも明らかでなければならない。 - 研修や人財採用の再設計
研修や人財採用手法は、新たに必要になるデジタル及びデータ分析スキル、自動化設備と協働するオペレーターに求められる要件、デジタル・マニュファクチャリングのユースケースに対する各地域リーダーや生産拠点のコミットの重要性に照らし、再設計する必要がある。 - 目標とするIT/OT全体像とロードマップの策定
最初のユースケースが成果を生み始めたら、次は、目標とするIT/OTの全体像や、目標達成までのロードマップを作る必要がある。これは、無駄な重複や冗長性を省き、長期にわたりデジタル・マニュファクチャリングの可能性を最大限引き出すために不可欠である。
より詳細な考察をお読みになりたい場合は、実践的指針や事例を豊富に含むローランド・ベルガーのレポート本編(英語版のみ)をご覧ください。
Register now to download the full study on “Whatever happened to Industry 4.0” including key insights, an outlook on the developments of the automotive industry as well as use cases for respective players within the industry. Additionally, you'll get regular insights into automotive topics.